How simulation is used in automotive design to decarbonize the industry
With transportation responsible for a significant percentage of global CO2 emissions, simulation technologies can be applied to all aspects of vehicle design to enable rapid innovation for greener vehicles.
A simulation workflow that progresses from concept design to detailed multi-physics analyses can assist in rapid design cycles necessary to meet the challenges of the climate crisis. Image credit: Ansys.
Together with Ansys, a developer of simulation software, we are creating a series of content about the technologies that make sustainable transportation possible. Read the foundation article of the series here, and our introduction to the Indy Autonomous Challenge here.
This article scans the automobile, examining how and where different simulation tools are used to design and test vehicle components and systems.
The decarbonization challenge
With the 2°C challenge from the Paris Agreement looming, decarbonization in transportation is a must. The design, development, and implementation of zero-emission vehicles must be expedited, which can only be achieved through exponential innovation. In addition to overall improvements in vehicle design and efficiency, an understanding of CO2 emissions through a car’s life cycle is required in order to reduce emissions with precision and pace.
At all stages of vehicle design, from aerodynamics to battery management system testing, simulation enables rapid, risk-free testing and development. Development in simulation reduces design lead times and increases time to market.
Automotive manufacturers are facing entirely new challenges as they develop electric vehicles with longer ranges, internal combustion engines with better efficiency, and autonomous vehicles that will disrupt the vehicle ownership paradigm. As supporting technologies emerge, such as embedded machine learning, 5G, and new methods of manufacturing, carmakers must innovate at a pace previously not experienced.
In this article, we explore the multitude of ways simulation is used by automotive designers to test and develop new ideas. We start with the body of the car and scan through engine design, battery system testing, and finally, advanced driver assistance features and autonomous vehicles.
Body design
Aerodynamic vehicles assist in reducing our reliance on fossil fuels by making internal combustion engines (ICEs) more fuel-efficient and improving the range and performance of electric cars. However, aerodynamic designs also require features for body strength and safety, such as a rear spoiler to prevent lift.
Aerodynamics
Engineers use computational fluid dynamics (CFD) analysis combined with three-dimensional (3D) modeling to optimize car shapes. If we take the example of the rear spoiler, researchers looking to extend the safety limits of fast-moving cars used simulation software to predict vehicle behavior according to the rear wing (spoiler) position.[1] The car, along with various movable “aerodynamic elements,” was modeled in 3D for CFD simulation, which was validated using actual wind tunnel test data, including forces and flow behavior. With an accurate CFD model, the wing’s angle of attack could be optimized in a simulated flow field, as if the car were traveling at 144 km/h, followed by braking and cornering analyses. With the combination of road testing, lab experiments, and simulations, engineers were able to design aerodynamic features that could be electronically positioned depending on the driving activity. Using the simulation software ultimately provided them with the ability to design a spoiler that maximized the car’s safety and speed, no matter the driving behavior.
The side mirrors of cars present an obvious challenge to aerodynamics, while areas on the hood may have hidden opportunities for improvement. CFD software can be used in both of these cases to automatically optimize the geometry for less drag.[2] Similar to the spoiler example, a 3D car model is subjected to aerodynamic forces to simulate driving on the road at various speeds and conditions. Engineers can use the adjoint solver for the shape optimization of hard-to-improve features, where slight geometry changes can reduce drag after only a few iterations. Thanks to the complex data set created from the simulations, design goals can be attained in a short time, compared to physical testing.
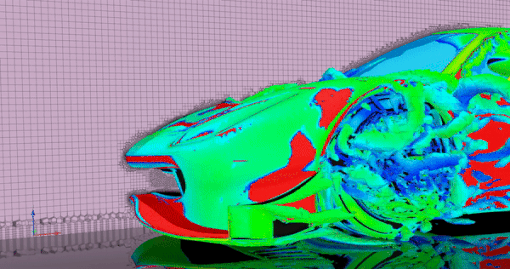
Crash testing
Crash testing has been around since the 1930s leading to safer cars and the introduction of the seat belt.[3] Specifically, crumple tests are designed to assess the car’s reaction to impact. Physical prototype tests to assess crumple require intricate instrumentation, high-speed data acquisition, and multiple car prototypes (which are immediately destroyed).
While physical testing is still a crucial part of automotive development, its timing can be pushed closer to the final stage, thanks to huge innovation in simulation. Finite element analysis (FEA) can now be combined with actual crash data to predict the results of a potential accident with a simulated impact.[4] The 3D vehicle model goes through simulated crumple tests to assess the car’s ability to keep the occupants safe and provide insights on how to improve the design to increase safety while maintaining low weight and other design aspects. Crash tests like the crumple test can be run in the initial stages of design, saving significant time and money associated with physical crash testing on actual vehicles.
Crash simulation and analysis software engages with explicit methods for highly nonlinear scenarios. Models can be created with 3D design tools and subsequently optimized with simulation tools for FEA and CFD, yielding a vehicle body design that is both fuel-efficient and structurally sound.
Internal combustion engine design
Drivers want high power and torque combined with good fuel economy, and the same can be said for car manufacturers aiming to improve emissions. When it comes to engine design, efficiency and performance do not necessarily go hand in hand. This trade-off is balanced through detailed analyses of the whole engine system. In addition to ensuring the structural integrity of an engine through FEA, engineers aim to improve the gas flow from the intake through the exhaust pipe.
For example, CFD comes into play again when analyzing the in-cylinder flow. Volumetric efficiency (maximizing the gas flow) along with the motion of the gas (swirl and tumble) can be predicted through 3D modeling and simulation with CFD simulation tools such as Ansys Fluent. Engine parameters, such as valve timing, port design, and piston geometry, can then be optimized for efficiency and performance.[5]
The chemistry inside the engine cylinder is a major factor in the production of CO, NOx, soot, etc. In addition to the prediction of tailpipe emissions, chemical modeling helps engineers design for improved combustion, alternative fuels, and added technology, such as turbocharging.[6]
Ansys Forte can apply CFD with a mesher and chemistry solver to internal combustion engines (ICEs) specifically to simulate combustion. The fuel spray pattern can be modeled and validated as part of this process.
Towards camless engines
Another effort towards more efficient ICEs is the elimination of the valve cam. A typical ICE valvetrain involves a camshaft mechanically driven by the engine. The timing of valve opening and closing events depends on the fixed cam profile that is optimized for engine performance and efficiency. However, variable valve operation can yield improved efficiency over the entire engine operating range. The camless approach removes the limitations of the cam, allowing each valve to be controlled individually, for example, through pneumatic actuators. If applied to a current engine, camless technology may provide 30 percent more power and torque and up to 50 percent better economy.
Researchers have applied simulation tools to explore the endless options of valve timing enabled through camless valvetrains. In one study by Zhang et al. from the Nanjing University of Science and Technology, CFD analysis was performed to obtain the load profile on an exhaust valve during operation, and then an electrical load simulator applied load on an actual valve for future control strategy development.[7]
From crankshaft fatigue strength to in-cylinder fluid dynamics, simulation technologies are key to the design of more efficient ICEs as we work towards emission goals. While the path to ICEs being totally phased out is clear. The effort to make them as efficient as possible until this time is key and will need to be a priority for all automotive players.
Hybrid and Electric Vehicles
As we transition from the ICE to the fully electric vehicle (EV), the hybrid electric vehicle (HEV) has been a popular choice for the environmentally conscious driver as well as manufacturers complying with new emissions regulations. Hybrids require the complex integration of various components, including the ICE and the battery, to achieve better efficiency while maintaining performance goals. Systems simulation and automated design processes are crucial to the electrification of powertrains.[8]
A zero-emissions EV removes the ICE from a vehicle but instead involves the complex design of a battery with trade-offs – performance, safety, size, cost. Various simulation tools give engineers the power to balance these trade-offs without extensive lab or field testing. Temperature, for instance, is a major factor in battery safety. Various simulation software options offer tools to simulate battery thermal management such that the designer can apply cost-effective yet sufficient cooling.[9] In addition to high temperatures, batteries must withstand impact, vibration, and other stresses, where FEA is invaluable in the early stages of design. Similar to the in-cylinder chemistry of the ICE, the electrochemistry of an EV battery can be analyzed through CFD simulations.
While an EV has no tailpipe emissions, an EV battery presents a significant end-of-life waste problem. An estimated quarter-million tons of EV battery waste results from a year’s worth of EV sales.[10] To combat this, battery design needs to now focus on longer life cycles, reuse, and recycle. For longer life, batteries need reliability and durability, and simulation tools offer FEA options to assess a battery’s thermal stresses and responses to vibration and impact, allowing for design tweaks that incrementally improve the overall system. Simulation is essential to achieve these goals to make a dent in the rate of battery waste production.
Whole-vehicle simulation
While the power system and aerodynamics are major factors in vehicle efficiency, we cannot forget about the impact of other components, such as the transmission, accessories, and tires. In addition, driving behavior has a significant effect on efficiency, and aggressive driving accounts for a 10–40% drop in fuel economy.[11] The same simulation tools for FEA, CFD, etc., can optimize these component designs individually before simulating the vehicle as a whole in real-world scenarios.
Driving simulators apply systems simulation with driver, model-, software-, and hardware-in-the-loop approaches, which let us see how the vehicle performs overall in various situations.[12] Engineers can easily vary component parameters, such as tire rolling resistance and transmission gear ratios, in different driving environments.
Along with the zero-emissions goal, vehicle safety is of utmost importance, with 94% of crashes caused by human behavior.[13] Advanced Driver Assistance Systems (ADAS) are being developed to address both issues of efficiency and safety. New cars are coming out with features like blind-spot alerts and virtual cameras, as well as more advanced autonomous capabilities like Tesla’s Autopark.
Driving simulators are key to designing these features, optimizing them for various scenarios, including rainy conditions, stop-and-go traffic, and mountain driving.
Ansys VRXPERIENCE offers a headlamp module, above, that assists designers to validate intelligent lighting systems.[14]
Simulation in developing autonomous vehicles
We cannot talk about ADAS without mentioning the ultimate goal of autonomous driving. While cars are currently being equipped with ADASs that approach Level 3 autonomy, fully autonomous vehicles will take us to the highest Level 5.[15] Simulation is essential in the development of autonomous vehicles, specifically to train their artificial intelligence (AI) systems. Additionally, simulation can assist in autonomous programs recognize and respond to various aspects of the car’s environment including objects such as cyclists as well as other driving conditions such as drag and tire wear.
Innovating through competition
The Indy Autonomous Challenge (IAC) is a year-long university challenge where teams are required to build an autonomous driving system from scratch before testing it using modified Dallara race cars in a high-speed autonomous race. The race enables the next generation of engineers to undergo an incredible learning experience while developing autonomous driving systems that could one day be part of commercial vehicles. The next stage of the challenge is a simulation race on June 30. See our full preview of the IAC Simulation Race here.
Ansys enables simulation to be both a guiding principle and design tool
Ansys understands that the speed of innovation in the transportation industry must be rapidly increased to meet the challenges of the climate crisis. The Ansys software suite enables engineers and designers to engage with simulation from conception through to the minute detail of vehicle design and testing. For the vehicle body, FEA with tools like Ansys Mechanical and CFD using Ansys Fluent can calibrate the exterior for solid aerodynamic performance. While tools such as Ansys Forte can provide insight and improvement within the car’s engine including assessments of the in-cylinder chemistry. Ansys SCADE Suite enables the necessary shift to electric technology by optimizing the battery and engine management of the HEV and EV. Finally, countless tests can be performed on the entire vehicle model in the virtual world with driving simulators like Ansys VRXPERIENCE, moving the industry at an exponential rate to the zero-emissions high-performing vehicles of the future.
Summary
Decarbonization in the transportation industry can be achieved, but time is of the essence. Simulation is a tool that enables rapid innovation quickly and safely. Above, we scanned the vehicle, demonstrating how simulation software is used in all aspects of coherent automotive design.
This article was written by technical writer/editor and automotive engineer Kimberly Sweetland with editing by the Wevolver Team and Ansys Global Industry Director, Tarun Tejpal.
About the sponsor: Ansys
Ansys provides engineering simulation software used to predict how product designs will behave in real-world environments. Founded in 1970, Ansys employs more than 4,400 professionals, many of whom are expert M.S. and Ph.D.-level engineers in finite element analysis, computational fluid dynamics, electronics, semiconductors, embedded software, and design optimization.
References
1. Kurec K, Remer M, Broniszewski J, Bibik P, Tudruj S, Piechna J. Advanced Modeling and Simulation of Vehicle Active Aerodynamic Safety. Journal of Advanced Transportation. 2019;2019:1-17.
2. Aerodynamic Car Body Shape Optimizations & Design | Ansys. Ansys.com. 2021 . Available from: https://www.ansys.com/blog/how-aerodynamic-shape-optimizations-simplify-car-body-design
3. Wheel T. How Did Car Safety Crash Tests Originate? The News Wheel. Available from: https://thenewswheel.com/how-did-car-safety-crash-tests-originate/
4. Car Crash Simulation | Make Software, Change the World! | Computer History Museum . Computerhistory.org. Available from: https://www.computerhistory.org/makesoftware/exhibit/car-crash-simulation/
5. Sushma H, K.B J. CFD modeling of the in-cylinder flow in Direct-injection Diesel engine. International Journal of Scientific and Research Publications. 2013;3(12).
6. Coble A, Smallbone A, Bhave A, Mosbach S. Implementing Detailed Chemistry and In-Cylinder Stratification into 0/1-D IC Engine Cycle Simulation Tools. 2011;.
7. Zhang L, Liu L, Zhu X, Xu Z. An Electric Load Simulator for Engine Camless Valvetrains. Applied Sciences. 2019;9(8):1591.
8. Electrified Powertrain System Integration | Ansys. Ansys.com. Available from: https://www.ansys.com/applications/electrified-powertrain-system-integration
9. Battery Modeling and Simulation Software | Ansys. Ansys.com. Available from: https://www.ansys.com/applications/battery
10. Peak Performance for an Electric Vehicle | Ansys. Ansys.com. Available from: https://www.ansys.com/dimensions-magazine/fall-2019/peak-performance-for-an-electric-vehicle
11. Many Factors Affect MPG. Fueleconomy.gov. Available from: https://www.fueleconomy.gov/feg/factors.shtml
12. Hyper-Realistic VR Driving Simulator | Ansys VRXPERIENCE. Ansys.com. Available from: https://www.ansys.com/products/av-simulation/ansys-vrxperience-driving-simulator
13. Administration N. Automated Vehicles for Safety | NHTSA. Nhtsa.gov. Available from: https://www.nhtsa.gov/technology-innovation/automated-vehicles-safety
14. Advanced Driver Assistance Systems (ADAS) & Autonomous Vehicle Simulation Software. Ansys.com. Available from: https://www.ansys.com/products/av-simulation
15. Top 3 Challenges to Produce Level 5 Autonomous Vehicles | Ansys. Ansys.com. . Available from: https://www.ansys.com/blog/challenges-level-5-autonomous-vehicles
Ansys provides engineering simulation software used to predict how product designs will behave in real-world environments. We offer a comprehensive software suite that spans the entire range of...
Using contact mechanics analysis to solve the toughest problems in engineering
8 minutes read
Shocks, Drops, Smashes, and Crashes: How to Overcome Tough Structural Challenges
8 minutes read
Using heat transfer simulation to engineer a rocket-launching balloon
10 minutes read