Future Trends in 3D Printing with Wear-Resistant Plastic Materials
Article #6 of The Engineer’s Guide to 3D Printing with Wear-Resistant Plastic Materials.
This article is a chapter from our comprehensive report on 3D printing with wear-resistant plastics. If you want to dive deeper and access the full report, we invite you to download it below. Don't miss out!
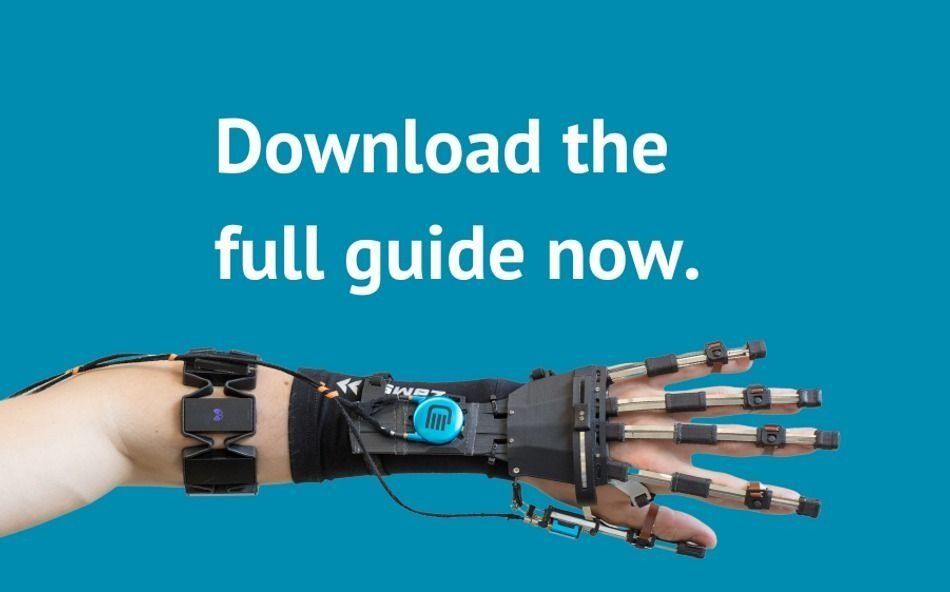
Low-friction 3D printed components
The industry has come a long way since the early days of 3D printing. Not only have 3D printer hardware and software technologies advanced significantly—with greater precision, faster print speeds, and better consistency—but the range of printable materials has grown enormously—and continues to do so. It’s been this expansion of 3D printing materials that has really driven additive manufacturing’s adoption across a wider range of industries and for more and more end-use applications.
The German company igus has played an important role in developing new 3D printing plastics, leveraging over 50 years of experience making functional polymer parts to create exceptionally wear-resistant materials. The company has carved out a specific niche for itself in the additive market, offering a range of strong, low-friction filaments, powders, and resins engineered for moving and sliding applications.
These materials have already created many new applications possible, such as finger joints for an exoskeleton and a special adaptive steering wheel slider, whose design would have been near impossible to realize using conventional methods. The materials’ unmatched sliding properties (enabled by special lubricant additives) have allowed igus customers to create low-friction components and assemblies that rival injection molded parts in terms of wear resistance and function. But this is really just the beginning for igus’ 3D printing journey, and for 3D printing in general. The potential and possibilities are endless.
What’s on the horizon?
Below are some trends that are taking off in the realm of 3D printing that are particularly relevant for wear-resistant polymers like iglidur and igumid materials for SLS, FFF, and DLP.
Scalable production
One of the biggest trends across the additive manufacturing industry today is the growing viability of 3D printing as an industrial end-use production process. Once a technology used strictly for prototyping (or hobbyist-grade parts), 3D printing is now broadly used across industries like automotive, aerospace, consumer goods, electronics, energy, medical and more, for everything from prototyping, to tooling, to end-use parts.
Material variety is central to this trend, as it offers users a wider range of properties to choose from. For instance, the growing availability of ESD 3D printing materials, such as iglidur i8-ESD, are opening up applications in the electronics and semiconductor industries, while tribologically optimized materials can be used to print inherently lubricated parts for various assemblies.
At the same time, a more consistent 3D printing process and the advancement of automated workflows are empowering manufacturers and 3D printing services alike to scale their production more easily. This means 3D printing will become more popular for larger production volumes, such as series production or mass customization.
Intelligent 3D printed parts
An emerging trend with incredible potential across many industries is the creation of intelligent 3D printed components that can gather usage data or alert users when there is a flaw or weakness in their performance. Using conductive 3D printing materials and multi-material 3D printing platforms, sensors can be embedded directly into a 3D printed geometry to impart these special functions.
igus engineers have already developed smart 3D prints, such as an intelligent bearing with sensors that can detect overload and issue predictive maintenance alerts. But the trend doesn’t end there: researchers at MIT are currently investigating the ability to 3D print sensors into rotational mechanisms, which will allow the parts to sense their movement.
The benefits of being able to directly print sensors into a part are enormous. If parts can sense their performance over time, users can more easily anticipate when maintenance is required, saving time and costs associated with breakages or system downtimes. It could also open up product innovations. For example, MIT prototyped a smart desk lamp that changes color and brightness based on part rotation.
Greater accessibility
As adoption and demand for wear-resistant, high-performance materials grow, the cost of materials will continue to decrease. This is because the cost for raw consumables will be driven down as production volumes rise (i.e. economies of scale). The lower cost of materials will then in turn further drive adoption of 3D printing and make the technology and high-performance materials more accessible.
The affordability trend is also driven in part by the cost of hardware, particularly engineering-grade machines capable of processing high-temperature and high-performance materials. Today, it is possible to purchase a high-temperature FFF 3D printer with nozzle temperatures up to 500 °C in the range of $25,000, which makes materials like iglidur polymers available for a wider user base.
Ultimately, lower entry costs for adopting 3D printing and the lower cost per part unlocked via cheaper material costs will make additive manufacturing increasingly competitive with more traditional manufacturing techniques, like injection molding, and lower the entry barrier for more users.
Sustainability
Sustainability has become an increasingly important topic within the 3D printing industry, and for good reason. Issues like plastic pollution and carbon emissions are tied to manufacturing and much must be done to curb the industry’s impact on the environment. Across additive manufacturing, sustainability is therefore a leading trend, and many innovative solutions are being explored and implemented.
At igus, the company is aiming to make all its production facilities CO2-neutral by 2025, employing tactics like clean energy sources and recycling programs to cut its ecological impact. The company’s self-lubricated polymers, including its range of 3D printing materials, also present a unique opportunity on the sustainability front. Every year, 27 million tons of grease end up in our environment, which leads to problems like water and land contamination. By turning to igus polymers that don’t require external lubrication, it is possible to cut back on grease consumption. Furthermore, due to the materials’ high durability, bearings, gears, and other components can have longer functional lives.
Of course, there is more to be done, which is why many polymer 3D printing providers are investing in things like greater process efficiency, material usage efficiency, and material recycling to create a greener future for additive manufacturing.
The future is bright for wear-resistant materials.
As we’ve seen, wear-resistant 3D printing polymers, such as those developed by igus, offer specific benefits to additive adopters in industries like automotive, industrial goods, and medical. As awareness of these materials grows and as igus continues to develop more materials and support new applications, the potential for high-performance polymers will only rise.
To learn more about igus’ 3D printing material range or to place an order for 3D printed parts, get in touch with the team today.
The Engineer’s Guide to 3D Printing with Wear-Resistant Plastic Materials
Explore the transformative world of 3D printing as we delve into the intricacies of using wear-resistant plastic materials. This guide offers engineers a comprehensive overview of material properties, applications, and best practices. Unlock the potential of durable plastics and revolutionize your manufacturing processes.