Palletization and depalletization of large ABS parts
The customer, an automotive manufacturer, needed an automation solution for the palletization and depalletization of large ABS parts. They decided on a solution where one vision-guided robot operates both processes.
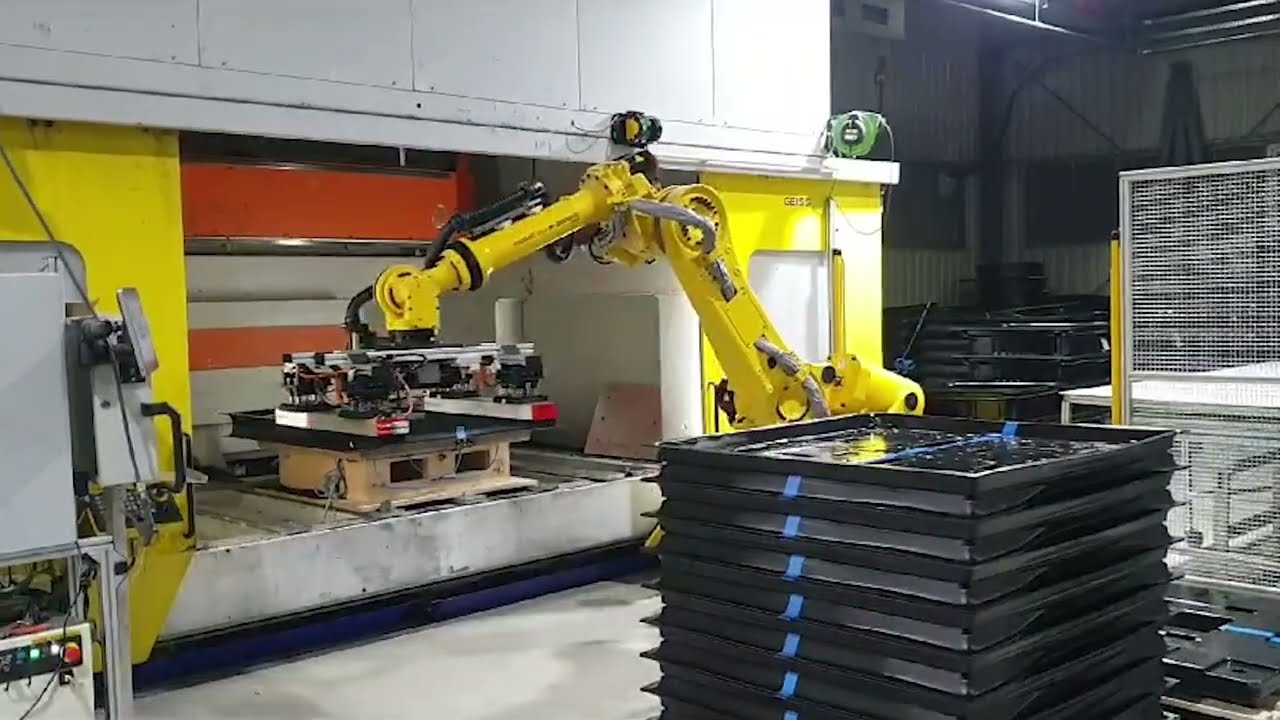
Palletization and depalletization of large ABS parts
Partner:
Challenge:
The customer, an automotive manufacturer, needed an automation solution for the palletization and depalletization of large ABS parts. They decided on a solution where one vision-guided robot operates both processes.
Solution:
Locator Studio + PhoXi 3D Scanner
The solution for palletization and depalletization consists of 2 different picking locations with 2 independent production flows:
A) Palletization – the ABS parts are taken from an output conveyor and placed on a pallet
B) Depalletization – the parts are picked from the pallet
The FANUC R-2000iC/210F Robot, navigated by Photoneo PhoXi 3D Scanner and Locator Studio, serves both locations. First, it picks the ABS parts from an output conveyor of a thermoformer press and stacks them on a pallet. The pallet is then taken to a cooling area. The height of the full pallet is ~1400-1500 mm from the ground.
The cooled parts are then picked from the pallet and fed to a CNC machine for trimming the outer border (the excess material). After trimming, the parts are placed on another pallet.
Any of the 2 jobs can be active or inactive at a certain production stage (a few hours or days).
The robot can either work in location 1 (the conveyor) or in location 2 (the pallet) or in both locations at the same time. So one robot can serve 2 different robotic cells.
Both robotic cells can process 4 part types but only one model during a production cycle.
For instance, Heat RT on the conveyor for 7 hours and Heat FT on the pallet for 3 days, then Heat FT – Top/Lid on the conveyor for 2 days and Heat RT on the pallet for 14 hours, and so on.
Every time a part model is changed in a location, the operator activates the correct model for that location so the robot knows what to look for.
Discussion:
This automation solution increased efficiency as one robot can operate two different production flows simultaneously.
The robot is navigated by state-of-the-art 3D vision from Photoneo, providing a resolution of up to 3 Million 3D points and an accuracy of 25 – 500 µm across the different models.
Would you like to discuss your project with Photoneo? Contact them here.