Improving Offshore Operations with ROVs
Improve your offshore operations with ROVs. Find out how they can help detect potential problems and save you valuable time and money.
Oil & gas pipeline inspection conducted with underwater ROVs.
This article was first published on
www.deeptrekker.comRemotely Operated Vehicles (ROVs) are essential tools in offshore operations, providing critical support in underwater inspections, maintenance, environmental and asset monitoring, and more.
This article explores how ROVs improve the accuracy and efficiency of inspections, reduce operational costs, and provide a safer alternative for underwater missions in offshore applications within the maritime industry.
ROV Offshore Applications with Maritime
Oil and Gas Inspections
Offshore energy inspections are critical for identifying potential issues before they escalate into major problems, thus preventing catastrophic failures and environmental disasters. Effective inspections ensure that energy production operates safely, efficiently, and responsibly, preserving the integrity of vital infrastructure and protecting human lives and the environment.
The management of offshore assets and infrastructure is inherently complex, hazardous, and costly. Consequently, the use of ROVs is becoming the industry standard, as their advantages over traditional inspection methods are increasingly acknowledged. ROVs eliminate the need for scaffolding, sky-lifts, cherry pickers, and expensive helicopter aerial views. Moreover, ROVs minimize the need for inspectors to dive in hazardous conditions or perform rope-access work in dangerous heights or confined spaces, such as inside ballast tanks.
Platform and Rig Inspections
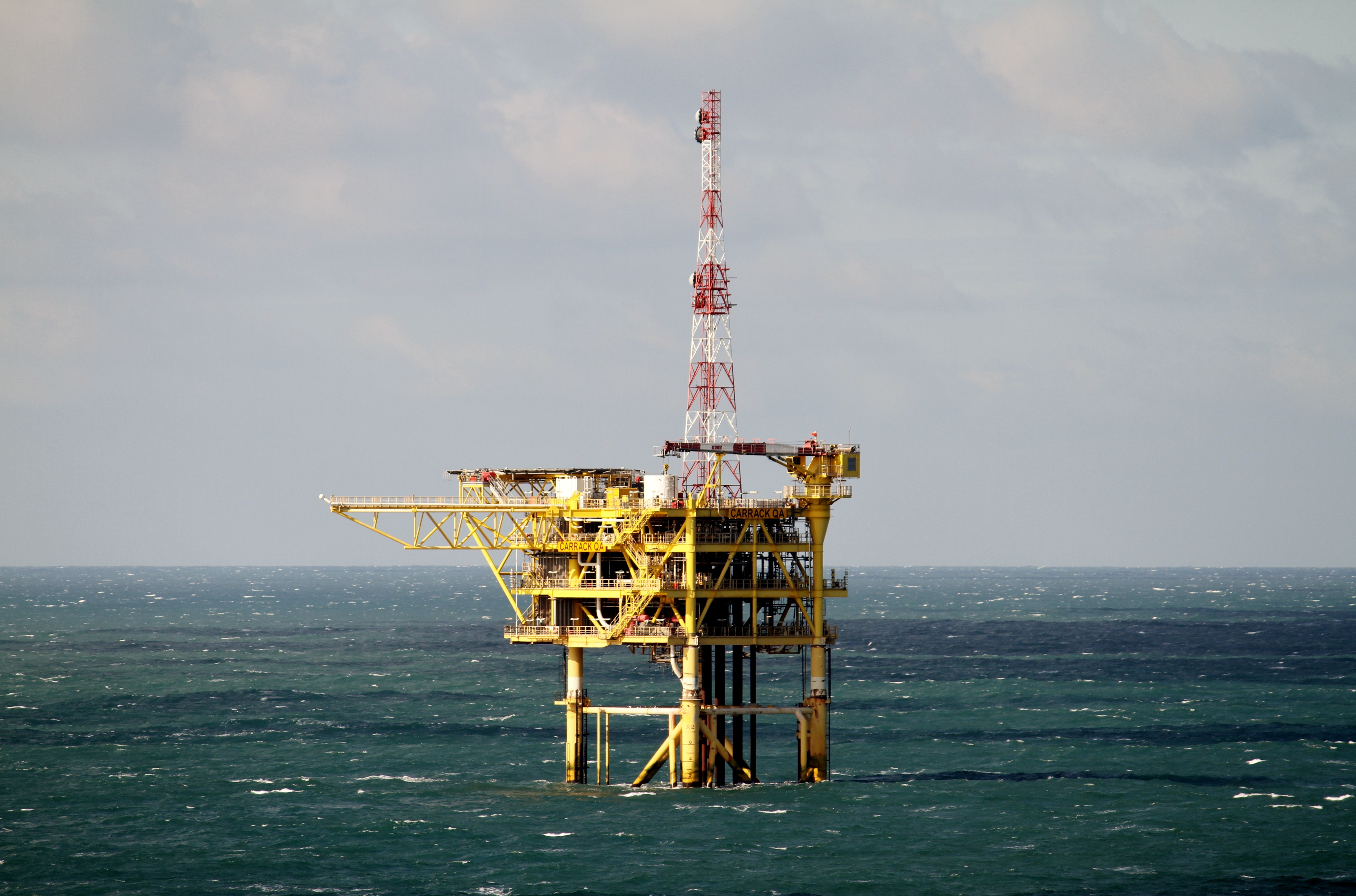
ROVs can be deployed to inspect various assets of offshore platforms, including:
- Platform legs
- Mooring systems
- Risers
- Cooling and ballast tanks
- Flare stacks
- Gas emissions in confined spaces
- Wellheads
By utilizing ROVs, operators can efficiently monitor for leaks, mitigate negative environmental impacts, and respond quickly to emergencies when they arise.
Pipeline Inspections
Offshore pipelines, which extend over vast distances on the seabed, and risers connecting the seabed to surface platforms, are prone to corrosion and damage. Regular monitoring and inspection are essential for maintaining safe and efficient operations. Traditionally, this required hiring and scheduling divers, which was both expensive and time-consuming.
ROVs offer a streamlined alternative, significantly reducing inspection times and costs. A single operator can deploy an ROV and complete an inspection within hours, compared to the weeks needed for divers. Additionally, using ROVs eliminates the risks associated with human divers, as working in marine environments presents numerous hazards.
FPSO Inspections
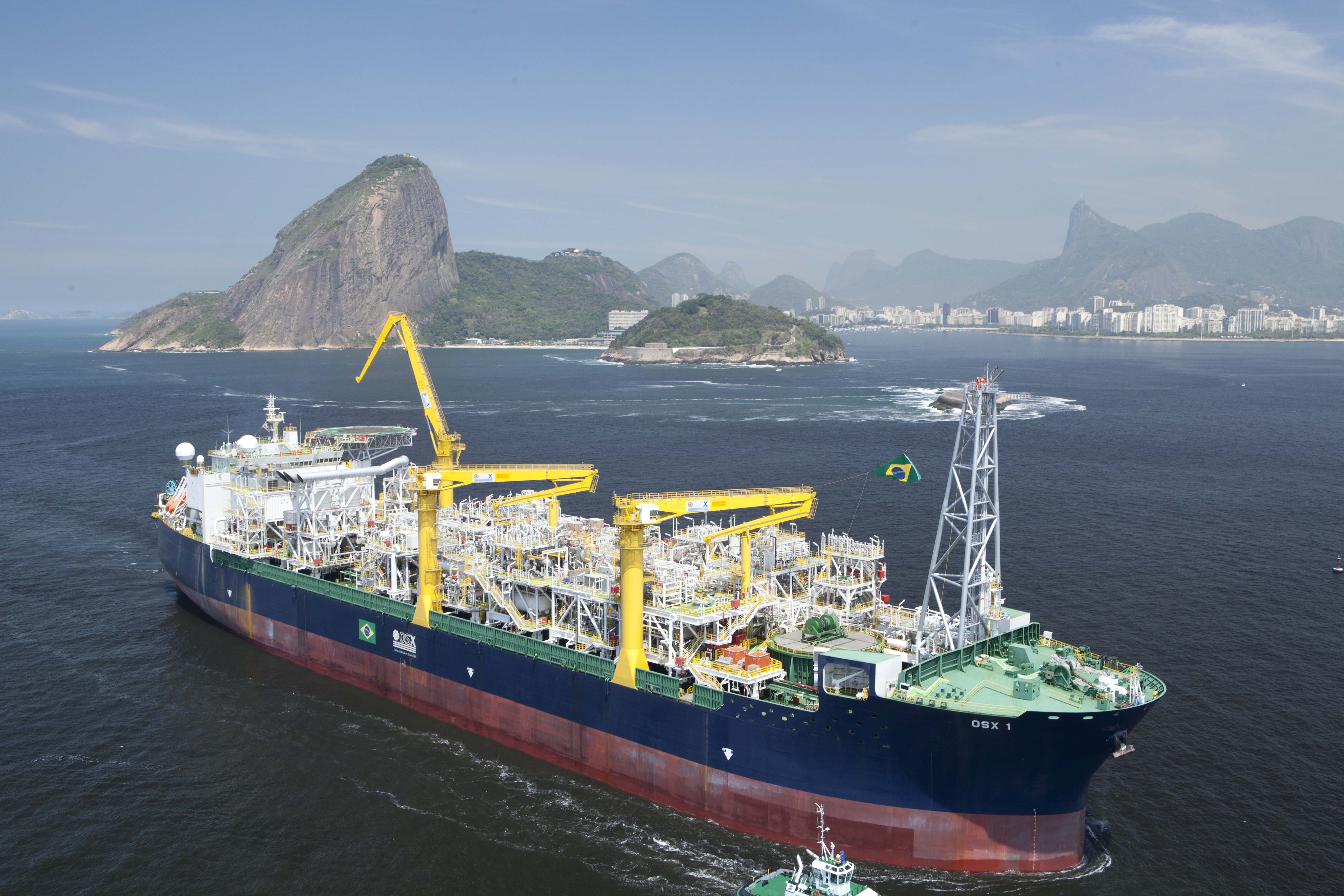
ROVs can conduct comprehensive underwater hull inspections in Lieu of Dry-Docking (UWILD) inspections, monitoring for biofouling, cracks, structural defects, corrosion, and the condition of protective coatings. They can also inspect other FPSO components such as rudders, propellers, and confined spaces like sea chests and ballast tanks. By avoiding the need for divers in hazardous environments, ROVs significantly enhance safety and reduce the risk of accidents.
Site Exploration
ROVs also play a key role in oil and gas exploration by assessing the suitability of new drill sites, providing real-time data and reducing the need for extensive preparatory work. They can survey and sample the seafloor, providing vital data for determining the viability of potential drilling locations.
This data is invaluable for evaluating the geological and environmental conditions of a site, helping to determine its suitability for drilling, allowing for the precise mapping of underwater terrain, identification of potential hazards, and analysis of sediment composition. Collecting samples enables geologists to assess the presence of hydrocarbon reserves and evaluate the environmental impact of drilling. Thorough assessments are essential for strategic planning, as it ensures that drilling operations are conducted in viable and safe locations, minimizing the risk of costly failures and environmental damage.
Subsea Construction and Maintenance
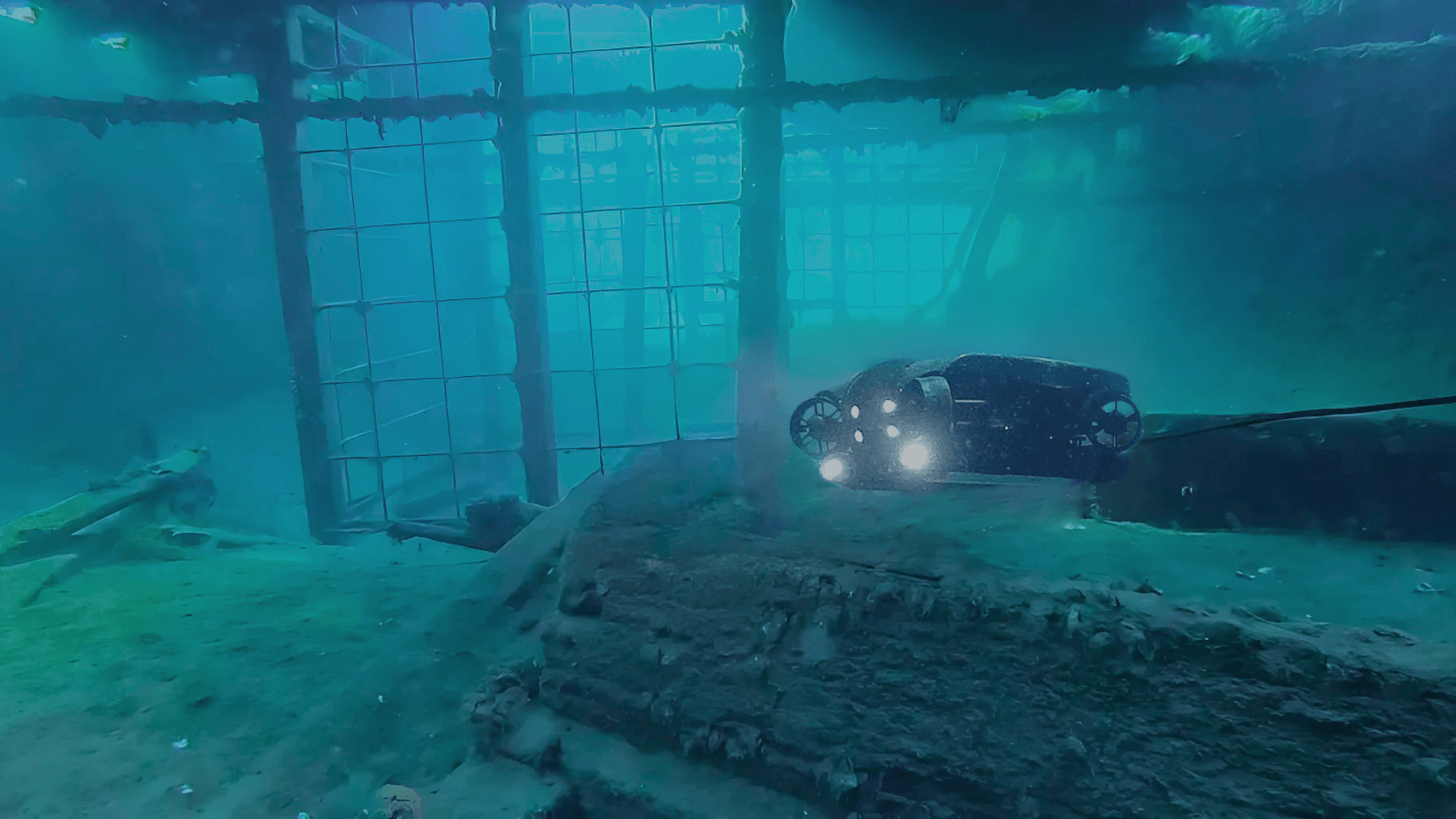
In subsea maintenance, ROVs offer notable advantages. They can stabilize equipment during repairs or installations and navigate confined spaces that might be challenging or unsafe for divers. Additionally, ROVs can perform temporary fixes, such as patching or stabilizing components, until permanent repairs can be scheduled. This capability not only facilitates ongoing maintenance but also reduces downtime and disruptions, ensuring that systems remain functional and safe throughout their lifecycle.
Wind Energy
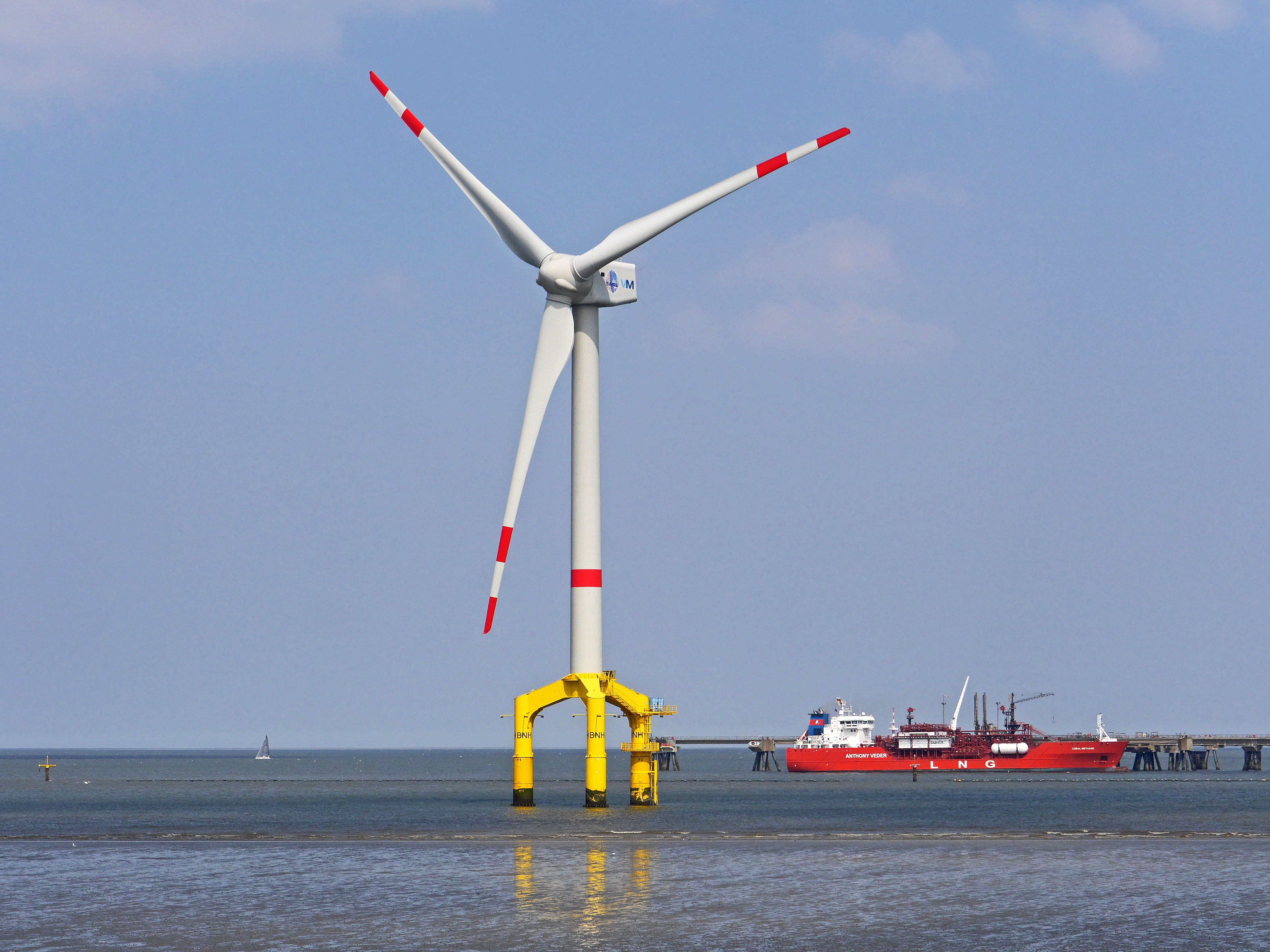
ROVs offer a solution to these challenges by providing comprehensive imaging of the entire turbine structure. They facilitate regular, thorough inspections, revealing internal corrosion, cracks, and other potential issues. This capability supports the development of efficient maintenance schedules and ensures a safer working environment by minimizing the need for human inspectors to access hazardous or hard-to-reach areas.
Maritime Archaeology
ROVs can be used to locate submerged historical sites with precision, capturing detailed images and video of artifacts that are often inaccessible due to depth or conditions. By providing a close-up view of shipwrecks and other submerged relics, ROVs help archaeologists assess their condition and develop strategies for preservation.
Additionally, ROVs are capable of creating detailed 3D models of archaeological sites through photogrammetry. By capturing high-resolution images from multiple angles, ROVs produce comprehensive digital representations of sites. These models allow for in-depth examination of structural details and provide permanent records for monitoring changes over time, supporting preservation efforts and enhancing research into cultural resources.
Search and Recovery
ROVs can provide valuable assistance in locating and, when possible, recovering missing people and objects such as boats, planes, and submarines. Equipped with high-resolution cameras and advanced sensors, ROVs can navigate challenging underwater environments, making them essential for conducting searches in conditions where traditional methods may be limited or impractical.
ROVs also gather critical evidence and data during these operations, aiding in investigations by providing real-time visual documentation and detailed information about the scene. This capability not only improves the accuracy of recovery efforts but also supports first responder teams by reducing their exposure to dangerous conditions. The use of ROVs enhances the efficiency, safety, and effectiveness of search and recovery operations.
Environmental Monitoring
Environmental monitoring is essential for offshore operations due to the potential impact that energy production can have on marine ecosystems. Accidents or faulty equipment can cause severe damage to the environment, making it critical to conduct regular and thorough inspections.
ROVs are ideal for performing detailed inspections of offshore infrastructure, allowing operators to identify potential issues such as leaks, cracks, corrosion, or spills before they become major problems. By utilizing ROVs, operators can detect and address these issues proactively, mitigating the risk of catastrophic damage. This proactive approach supports the integrity of offshore structures and reduces the likelihood of incidents that could have far-reaching environmental consequences.
ROVs also contribute to monitoring environmental impacts by evaluating species and habitats, conducting water and sediment sampling, analyzing water quality, and performing seafloor surveys. Additionally, ROVs aid in the recovery of ghost fishing gear - lost or discarded equipment that poses a threat to underwater ecosystems. They also assist in assessing the impacts of commercial shipping, such as the spread of invasive species, by inspecting hulls and other structures to prevent further ecological disruption.
Benefits of Using ROVs for Offshore Applications
The use of ROVs in offshore inspections is a game changer. Traditional methods are known to be quite complex, difficult, expensive, and dangerous. Advancements in technology and robotics have changed that, streamlining the process and making it much more efficient, safe, and affordable.
Here are just a few of the benefits that ROVs bring to offshore energy inspections:
- Cost - Reduce the need to hire commercial divers, buy or rent special equipment, schedule helicopters.
- Safety - ROVs handle hazardous tasks, collaborating with divers to reduce their exposure to dangerous conditions and improve overall safety.
- Efficiency - ROVs can examine offshore facilities much quicker than divers can, and can be deployed at any time, without the need to schedule inspectors or shut down systems.
- Easier Data Recording Capabilities - With cameras and data recording software, operators are able to compile inspection reports that illustrate an accurate history of asset status monitoring, which allows for more economical forecasting of routine repairs.
- High-Quality Imaging - ROVs feature enhanced 4K cameras (with color correction, auto white balance, turbidity filter, dewarping, and digital zoom), sonar, and location mapping for low-visibility conditions.
- Modular Add-ons - Easily incorporate tools such as manipulators and NDT sensors, such as UT thickness gauges and CP probes for comprehensive data collection.
How is the Offshore Industry Evolving with ROVs?
The adoption of ROVs in the offshore sector has surged dramatically. Since the 1980s, the use of ROVs has grown from around 500 units globally, being used primarily for industrial and military operations, to tens of thousands worldwide, reflecting their growing importance in offshore operations and maintenance. Companies across the industry are increasingly integrating ROVs into their operations, highlighting a shift towards more advanced, automated technologies.
This change is also reshaping the job landscape within the offshore industry. New career opportunities are emerging, such as ROV pilots, ROV supervisors, and Oceaneering. These roles involve operating and overseeing ROVs during offshore inspections and operations.
ROV Pilots operate ROVs to perform inspections and gather data. They often work for companies like Oceaneering, a leader in ROV operations. To become an ROV pilot, one typically needs specialized training and certification. The salary range for ROV pilots varies, but it generally falls between $60,000 and $90,000 USD annually, with potential for growth as the industry expands.
ROV Supervisors manage ROV operations, ensuring equipment is used effectively and safely. This role requires extensive experience and knowledge of ROV systems. Supervisors earn an average salary between $80,000 and $120,000 USD per year.
Oceaneering, a prominent player in the ROV industry, offers a range of roles from pilot positions to supervisory roles, setting a benchmark for others in the field. As ROV technology continues to advance, the demand for skilled professionals in this sector is expected to rise, offering promising career prospects for those interested in offshore operations.
The expected growth for careers in ROV operations is promising due to the increasing reliance on ROV technology in various offshore activities, including oil and gas exploration, renewable energy projects, and underwater infrastructure inspections. The demand for skilled ROV pilots and supervisors is anticipated to rise steadily over the next decade.
The Bureau of Labor Statistics (BLS) projects that employment in fields related to ROV operations, such as commercial diving and underwater welding, will grow faster than the average for all occupations. Specifically, the offshore oil and gas industry, along with the renewable energy sector, is expected to drive this growth.
This positive job outlook reflects the industry's shift towards more automated and remote technologies, enhancing safety and efficiency in offshore operations. As companies continue to adopt ROVs, the need for qualified professionals to operate and manage these systems will continue to increase.
Case Studies: ROVs in Offshore Applications
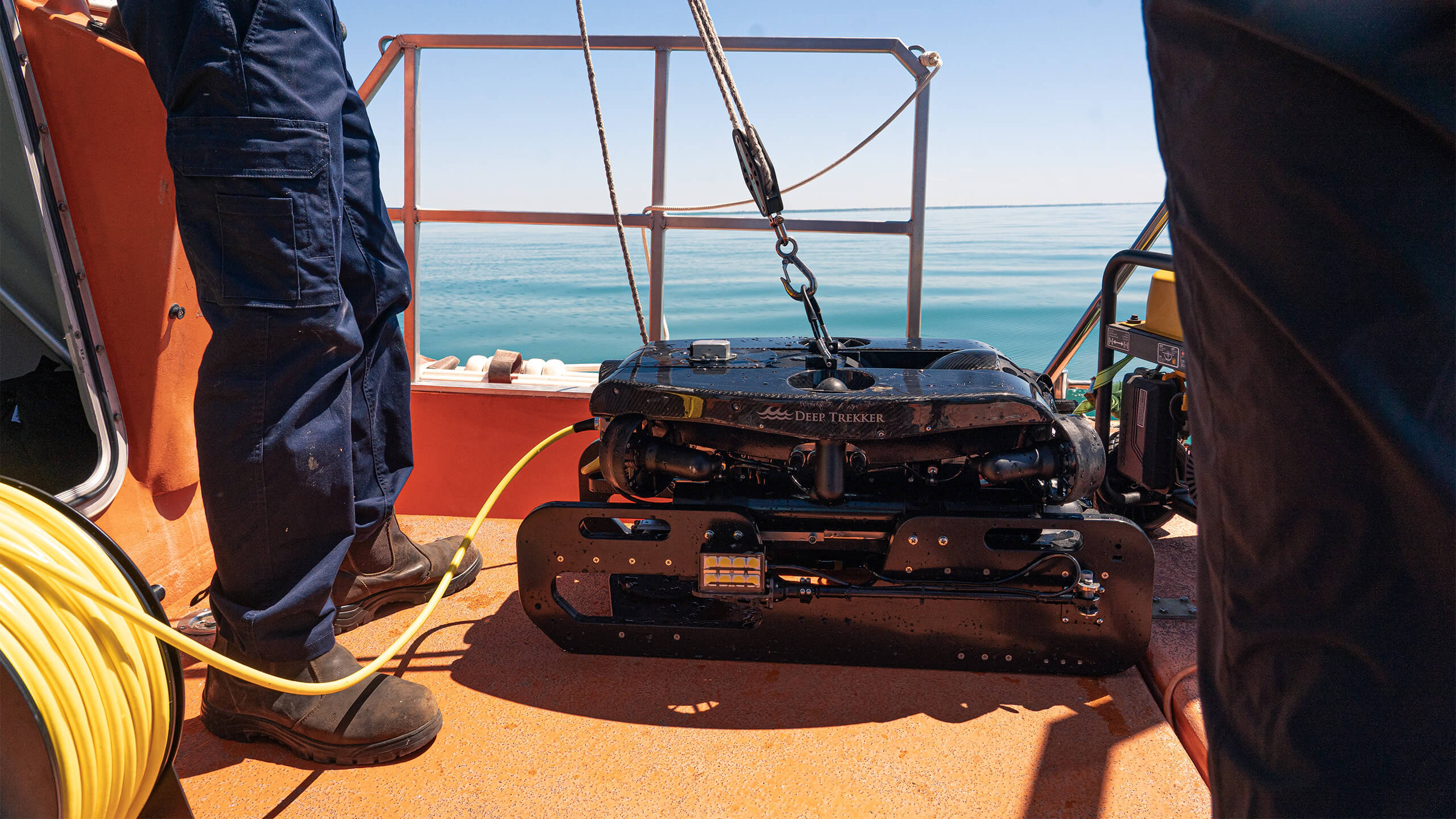
Miko Marine AS: Using ROV to Inspect Sea Chest Covers
Miko Marine AS, headquartered in Oslo, Norway, showcased their use of Deep Trekker ROVs in a significant marine salvage project. They designed and implemented cofferdam and sea chest covers using magnetic adhesion technology. This project aimed to improve seal integrity and water defense for an offshore drilling company. The system featured four Miko MAM permanent magnets, each with a holding capacity of up to 450 kg, providing a secure and immediate watertight seal without additional fastening mechanisms.
The covers were deployed off the coast of Haugesund, Norway, at a depth of 16 meters. An inspection ROV was utilized to assess the effectiveness of the covers externally, while an internal camera verified the absence of leakage.
Miko Marine also explained that, "When the job is finished, each magnet is simply freed by having its release lever lifted by a diver or ROV, so the cofferdam can then be retrieved."
Orange Force Marine: ROV Photogrammetry of Offshore Wellhead
Orange Force Marine Ltd. utilized a Deep Trekker ROV to generate a 3D photogrammetry model of a submerged wellhead for one of their clients. Known for its innovative marine solutions, OFM chose the Deep Trekker ROV for its reliability and precision in underwater inspections.
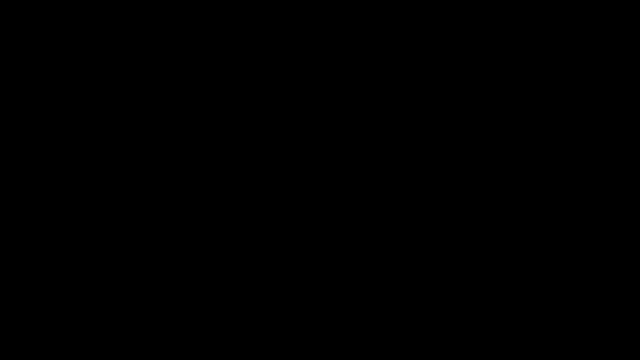
The process began with the deployment of the ROV to the wellhead site, where it captured a series of high-resolution images from various angles. These images were then processed using photogrammetry software to develop an accurate and detailed 3D model of the wellhead. Derek Niles, President at Orange Force Marine Ltd., remarked, "The clarity and stability of the ROV's footage were crucial in capturing the necessary data for an accurate model."
The resulting 3D model provided Orange Force Marine and their client with a comprehensive view of the wellhead's condition, enabling detailed inspections and analysis without the need for divers. This model supported better decision-making and maintenance planning, saving both time and resources. Derek highlighted the benefits, stating, "The precision of the Deep Trekker ROV allowed us to generate a model that exceeded our expectations, providing invaluable insights into the wellhead's structural integrity."
The Deep Trekker ROVs performance and ease of use were particularly appreciated by the team at Orange Force Marine. "The ROVs intuitive controls and rugged design made it an indispensable tool for our operation," Derek added. The success of this project demonstrates the value of integrating advanced ROV technology into marine inspection workflows.
Deep Trekker ROVs for Offshore Applications
Deep Trekker ROVs are designed to withstand the toughest conditions, featuring maneuverability, quick deployment, and ease of use, making them ideal tools for offshore applications.
The PHOTON is a lightweight mini observation class ROV, perfect for confined and hard-to-reach spaces, enhancing inspection safety and efficiency. This quickly deployable ROV can reach depths of 120 meters and is equipped with an ultra-high-definition camera with a rotating head, bright LED floodlights, and tether options up to 300 meters.
For operations requiring more payload capacity, greater depths, and modular options such as sonar imaging, the PIVOT and REVOLUTION models provide a robust suite of features.
With six vectored thrusters, these ROVs ensure peak stability and maneuverability. They are equipped with intelligent sensors, a 200-degree rotating ultra HD 4K camera head, BRIDGE integration, and modular tool add-ons, making them suitable for a wide range of tasks in challenging environments.
Investing in a single ROV can significantly reduce operating costs, potentially saving hundreds of thousands of dollars. These ROVs deliver accurate and thorough data of assets consistently, improving efficiency and safety in offshore operations by providing higher quality data and minimizing the need for human divers to enter hazardous spaces. This approach ensures the health of critical infrastructure and creates a safer environment for offshore workers. It’s a win-win for everyone, ultimately.
Versatile and Durable Solutions for Your Marine Projects
Deep Trekker ROVs, constructed from industrial-grade materials like stainless steel, anodized machined aluminum, and carbon fiber, are designed for versatility and durability in the harshest environments. Our team of industry professionals is available to provide expert guidance on integrating submersible robots into your projects across various applications, including underwater inspection, search and recovery, aquaculture, and environmental monitoring. Contact us for a customized quote tailored to your specific needs.