Industry 4.0 Technology Deep Dive
This expert-written eBook investigates the technological developments behind current changes in the way we manufacture.
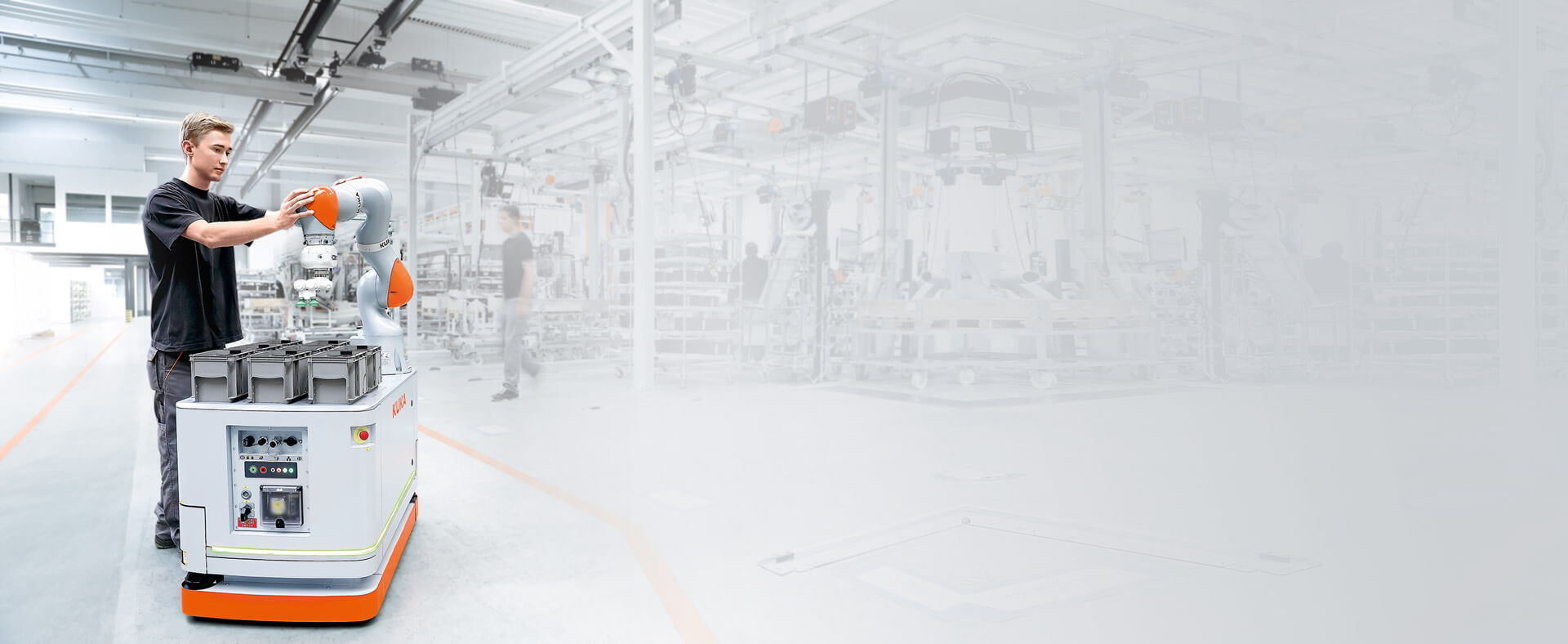
About the Contributors
John Soldatos Athens, Greece
- Honorary Research Fellow, IIoT, University of Glasgow.
- Adjunct Professor, University of Sheffield, Athens Tech Campus.
- Previously Adjunct Professor at the Information Networking Institute, Carnegie Mellon University.
Rodrigo Teles Strasbourg, France
- Ph.D. in Computer Science at the University of Strasbourg, focus on IoT.
- Member of the Network Research Team of the ICube Laboratory.
Sophie Laurenson Zurch, Switzerland
- Ph.D. in Biochemistry, Biophysics and Molecular Biology, from the University of Cambridge.
- Executive MBA, Business Administration and Management, the Smartly Institute. Previously Senior scientist and innovation manager at The New Technology Group of Abbott.
Neil BakerSydney, Australia
- CEO and Co-founder Medulla Research Associate, IoT and Smart Grid, Lancaster University.
- Ph.D. in Physics, on Nonlinear Optics, at the University of Sydney.
- Bachelor, Engineering Physics & Management at McMaster University.
Andreas BihlmaierKarlruhe, Germany
- Co-founder and CTO of Robodev Previously leader of the Cognitive Medical Technologies group in the Institute for Anthropomatics and Robotics - Intelligent Process Control and Robotics Lab (IAR-IPR). Ph.D. in Robotics from Karlsruhe Institute of Technology (KIT).
Adriaan SchiphorstAmsterdam, the Netherlands
- Technology journalist.
- MSc Advanced Matter & Energy Physics at University of Amsterdam and the California Institute of Technology. Previously editor at Amsterdam Science Journal.
Anish Jindal Lancaster, United Kingdom
- Senior Research Associate, IoT and Smart Grid, Lancaster University, UK.
- Ph.D. Computer Science and Engineering, Thapar University.
Mohammad RafieeOttawa, Canada
- Postdoctoral Fellow, Robotic Manufacturing, at the École Polytechnique de Montréal, Canada.
- Professor in Advanced Additive Manufacturing, Materials for Additive Manufacturing, and Smart Structures, at the University of Ottawa.
- Ph.D. Mechanical Engineering, University of Ottawa.
Per SjöborgStockholm, Sweden
- Founder of Aptomica.
- Founder of Flexibility Envelope.
- Creator and host of Robots in Depth podcast.
Get the Ebook
Executive Summary
Industry 4.0 can be understood as the fourth industrial revolution, heralded in through a convergence of technologies that lean heavily on continuous data gathering and artificial intelligence in a networked environment to present a new form of agile, responsive, and customizable manufacturing. Originally, the term was coined in Germany, where it is spelled as "Industrie 4.0."
This e-book, written collaboratively by experts in the fields of robotics, manufacturing, IoT, engineering, aims to provide an overview of the technologies that drive the current changes in the way we work and manufacture. It describes how Industry 4.0 came to be and dives into all the components that come together to create this new industrial paradigm.
Historical perspective and future possibilities on industrial revolutions
The beginning of machine-assisted linear production was defined by highly detailed specifications, a single or highly hierarchical system integrator, and the mass production of items. Changes to the product or system required a complete tear-down and rebuild. This type of system was only economically viable to large manufacturers, in big plants producing huge volumes. In contrast, Industry 4.0 applies to facilities of all sizes. An Industry 4.0 manufacturing facility collects data at all stages of its production process allowing it to make regular, intelligently informed decisions about productivity, safety, and efficiency. The exemplar of Industry 4.0 heralds in a new understanding of manufacturing that is agile, lean, highly customizable, and viable at all scales.
Artificial intelligence and data-driven insights in Industry 4.0
AI has been of interest to the manufacturing industry since the 1980s and has been applied across the entire production cycle from the planning and design phase, system and maintenance design, to its latest iterations in collaborative robots. Recent advances in sensors mean that all aspects of the factory can be under real-time continuous monitoring, generating an enormous amount of data. Advanced analytics provide the potential to convert these large datasets into actionable insights in real-time.
Manufacturing facilities have long been deeply embedded with sensors or all kinds, but significant advances in wireless network technologies now facilitate inter-sensor communications which are fundamental to the functioning of industrial IoT. These advances have also reduced the capital costs allowing access for smaller manufacturers.
The availability of relevant data and the systems to analyze it makes automation of some or all of the production process within a manufacturing facility possible. It offers control to operations of all sizes to understand its functions to a granular level without additional management or complex quality control. Companies wishing to meet the aspirations offered by Industry 4.0 will embrace a data-driven approach to both their facilities and approach to the market.
Hardware and human interfaces in the industry
A fundamental aspect of Industry 4.0 is the evolution and continuous improvement of robotic systems. Even as recently as a decade ago, robotics were accessible to only the largest of factories. Today robotics are being implemented into production facilities of all sizes. The evolution of robotics to more affordable, versatile, and easier to operate machines has also brought the collaborative robot, or ‘cobot,’ to the factory floor. These small, lightweight, and significantly cheaper robots work collaboratively alongside human workers to increase productivity, create safer work environments, and augment human quality control abilities.
Initially, these cobots acted as guides and heavy lifters, assisting humans with repetitive heavy labor, but have since evolved into active machines that can employ their ‘senses’ to work intuitively with humans on complex assembly tasks. Cobot makers and the manufacturing industry will need to collaborate cleverly to ensure the future development of these robots are enhancing work environments and sensitive to global employment demands.
As Industry 4.0 moves closer to its guiding goals of higher efficiency, flexibility, customization, and productivity with lower costs through automation, the factory workforce will shift from focusing on high physicality and low cognitive demanding roles to enhanced, more cognitively rewarding positions.
Conclusion
Industry 4.0 will continue to evolve and expand with both technological advances and broader adoption across industries. Increasing automation and data-driven manufacturing will have positive impacts on economies, productivity, and innovation while ushering in a new era of human-robot relations.
Continue Reading
Openly access the full e-book below. Or, alternatively read the individual chapters online:
- Part 1: Introducing smart manufacturing
- Part 2: Data-Driven Intelligent Production
- Part 3: Networks and Sensors
- Part 4: Evolving Industrial Robots
- Part 5: Flexible Manufacturing
About the sponsor: KUKA
KUKA is a global supplier of intelligent automation solutions. They offer everything from individual components to fully automated systems. KUKA was founded in 1898 in Ausburg, Germany, and currently has roughly 14,000 employees and sales of around 3.2 billion euro. Their mission is "making life and work easier."
On their website, KUKA provides more resources and a brochure about their vision on Industry 4.0 and the solutions they offer.