Ford's 3D Printed Jigs & Fixtures with BigRep Large-Format Additive Manufacturing
Learn how Ford optimized factory-floor tooling production with a 94% lead time reduction by introducing BigRep large-format additive manufacturing. Following an incredible success, Ford expanded their BigRep ONE’s use and needed more additive manufacturing capacity – leading to a BigRep PRO!
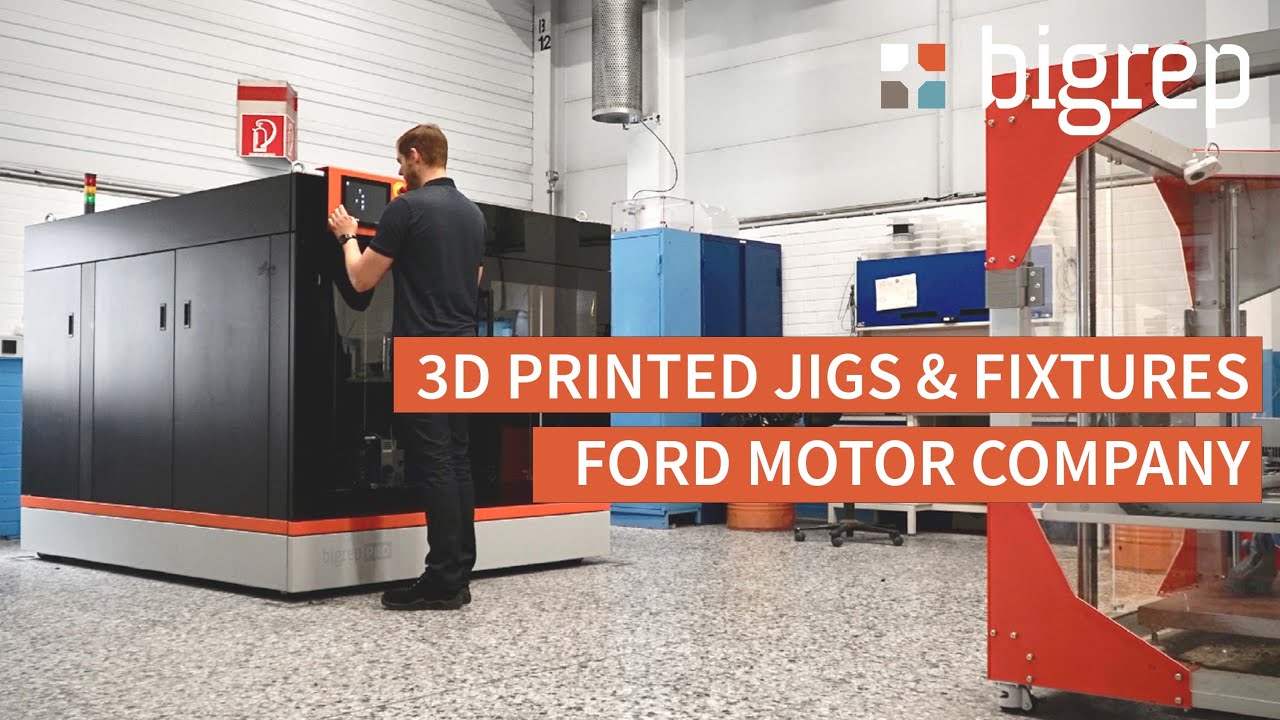
Ford optimized factory-floor tooling production with a 94% lead time reduction
This article was first published on
youtu.beHOW FORD OPTIMIZES MANUFACTURING WITH 3D PRINTED TOOLING
It’s no longer a secret that the automotive industry is a major adopter of 3D printing technology. Auto giant Ford Motor Company, based in the US with a worldwide presence, purchased its first 3D printer –the third SLA 3D printer ever to hit the market, in fact – in 1986.
The company’s only research facility outside the United States, Ford Research & Advanced Engineering Europe, opened in 1995, is dedicated to advancing the next generations of Ford’s vehicles and their manufacturing processes with additive manufacturing technology. As the company that pioneered the automotive assembly line, forward thinking is in Ford’s DNA.
Exploration of and investment into 3D printing has picked up for Ford in recent years, and most recently they’ve been going even bigger.
“3D printing is not a new technology, Ford has been using it for decades, but in the last years 3D printing became more and more relevant as a ‘real’ manufacturing technique,” says Lars Bognar, a Research Engineer in Advanced & Additive Manufacturing at Ford Research & Advanced Engineering, Europe. “That’s why Ford’s research activities in that field were increased. Now 3D printing plays a big role.”
From its start with SLA 3D printing Ford also moved to embrace additional additive technologies, including the BigRep ONE's FFF 3D printing capabilities. Working primarily on jigs and fixtures, tool tryout-parts, and manufacturing equipment, Ford’s BigRep ONE is used in many of the day-to-day activities.
The newer machine, the BigRep PRO, offers the same large build envelope with more advanced features. With the ability to print abrasive, engineering-grade materials, the BigRep PRO is designed for creating functional prototypes, composite tooling, and end-use products – making it a nice fit for Ford and for the automotive industry.
Download the full ebook here https://bit.ly/3ACza7e