Smart Packaging Explained
When we choose what to buy, we usually look at the expiration date, brand, quality seals, ingredients, and price. But how do you know if the manufacturer is fully honest – or that the product was properly stored during shipping or while on the shelf?
Illustrations by Dmitry Lisovsky for ITMO.NEWS
When we choose what to buy, we usually look at the expiration date, brand, quality seals, ingredients, and price. But how do you know if the manufacturer is fully honest – or that the product was properly stored during shipping or while on the shelf? The answer could lie in smart food packaging, which is designed to help us trace the real expiration date and prevent counterfeiting. So, what is smart packaging and what does 3D printing have to do with it? We asked Chantal Tracey, a PhD student at ITMO’s ChemBio Cluster and a member of SCAMT Institute’s 3D Printing of Functional Nanomaterials Group.
What is smart food packaging?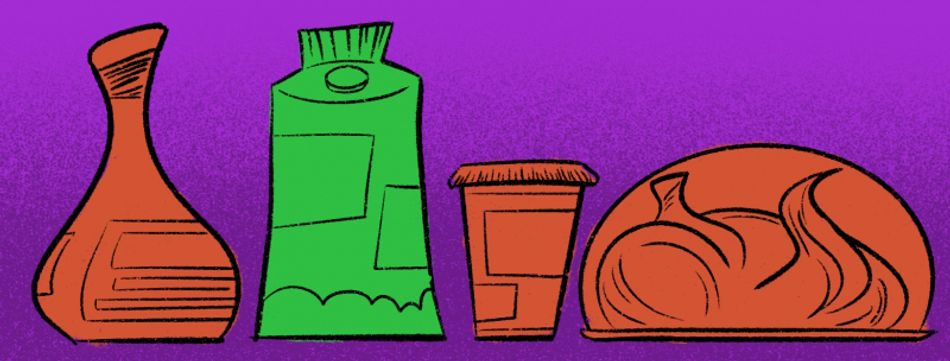
Consumers don’t always correctly read expiration dates and often treat products with caution, as they could be fake or improperly stored (thawed and frozen more than once, for example). Smart packaging is a solution to these issues: the built-in sensors and indicators monitor the freshness of the product, the packaging’s integrity, and even changes in external and internal conditions. Meanwhile, electronic tags on the packaging can help verify the product’s authenticity and help trace its location.
What are the things that make it “smart”?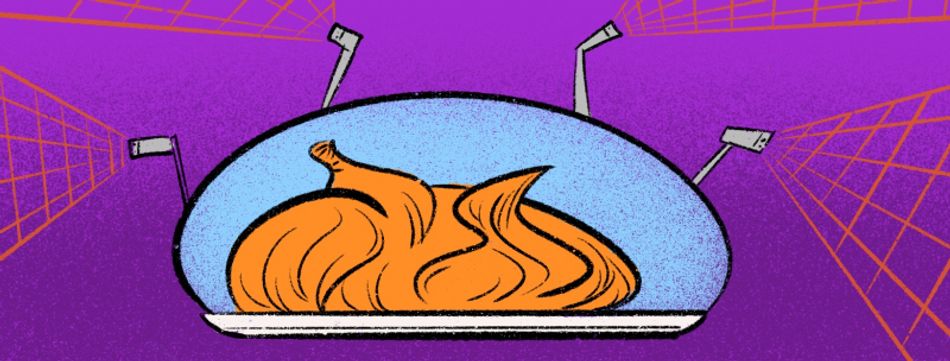
1. Sensors that monitor changes in the external environment. If the temperature or pressure changes, the sensors convert that data into electronic signals. This way, we can learn about the storage conditions and find out whether the packaging remains intact.
2. Indicators that change color depending on electrochemical stimuli. For instance, if the packaging is supposed to be hermetically sealed, the device will react to base atmospheric elements (carbon oxide, nitrogen, oxygen) that can only find their way inside if the packaging has been pierced, torn, or otherwise damaged. Such indicators can also react to gasses produced by bacteria.
3. Biosensors that react to cell components of microorganisms.
4. Electronic tags (RFID) consisting of an antenna and a microchip: these can simply glow or transmit data to other devices. They are used to track the movement of a product or inform the consumer about its ingredients, manufacturer, and so on.
How is data from sensors relayed to the consumer?
1. Changes in color
Colorimetric sensors consist of a solid substrate and a layer of dye. The dye changes color either upon contact with elements found in the environment or in the presence of gasses produced by microorganisms found in spoiled food.
The same goes for temperature and pressure sensors. When the indicator is affected by heat, cold, or impact, the color or location of the marking changes. That is, for instance, the working principle of the carbon-dot- and nanocellulose-based heat sensors developed at ITMO.
Another example are biosensors. These devices consist of a sensitive element (which contains a biological substance that reacts to microorganisms and their byproducts) and a converter that turns the reaction into light.
2. Tactile changes
There are special labels that can change their texture, such as turn coarse, upon contact with certain gasses.
3. Data
The packaging may be embedded with electronic tags that transmit information about the manufacturer and ingredients using NFC – and location data using GPS. By the way, researchers from ITMO have recently suggested a cheaper and more effective method of producing such tags.
Another solution are images printed with special “invisible” ink or randomly generated and applied with laser and carbon nanodots or holography.
Are there any challenges with the use of smart packaging?
As of now, the smart parts of smart packaging are produced using inkjet, gravure, and silk-screen printing. But there are drawbacks to such methods, including their high cost. Consumer surveys, at the same time, show that people aren’t willing to pay more than 10% above the usual price for products in smart packaging.
For this reason, researchers are working on new ways to produce smart elements. One possible solution is to 3D-print sensors, indicators, and electronic tags. This way, the packaging may be embedded with several elements at once – ones that are more sensitive than their conventional counterparts.
How does 3D printing solve these issues?
Unlike the usual methods, it lets us create lighter and more complex details. It is also a single-stage process and is almost fully automated. Besides, 3D printers are capable of creating complete systems out of different materials and don’t require costly additional equipment. The ink can be produced out of a wide variety of materials: metals, polymers, optically, electrically, or magnetically active particles, nanoparticles, biocompatible materials (chitin, nanofibrils, and cellulose nanocrystals), and biodegradable resins.
What does the printing process look like?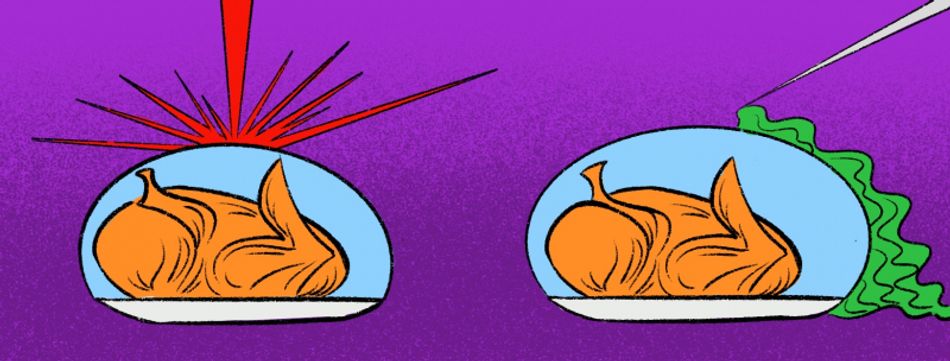
There are two methods: stereolithography and extrusion-based 3D printing.
1. Stereolithography
This is a process during which a mixture of liquid polymers and photosensitive additives are treated using pinpoint photopolymerization (solidification under the influence of light – usually, ultraviolet radiation). In order to create a three-dimensional object, the container with the mixture is moved in relation to the laser beam – or vice versa. This method is suitable for the production of small but highly detailed objects.
2. Extrusion-based 3D printing
With this method, a viscous solution, liquid alloy, or paste is applied onto a substrate using an injection head: each new layer fuses with the previous one and quickly solidifies. Just as in the case of stereolithography, either the injection head moves around the substrate, or the substrate around the injection head. This approach is suitable for systems that consist of different materials, but it is also quite time-consuming.
What can we expect to see in the future?
Despite the advantages of 3D printing, it still loses to 2D methods when it comes to the production of electronic elements: integrated circuits, antennas, transistors, electrodes, and so on. That is why researchers believe a combination of the 3D and conventional methods will allow them to print hybrid smart packaging as a whole, not as separate elements. If achieved, this technology will make the production process less costly and accelerate its adoption by manufacturers.
Based on a review paper written by the staff of SCAMT Institute:
Chantal Tracey, Aleksandra Predeina, Elena F. Krivoshapkina, Eugenia Kumacheva, A 3D printing approach to intelligent food packaging (Trends in Food Science & Technology, 2022).
Translated by Vadim Galimov and originally published by ITMO.NEWS